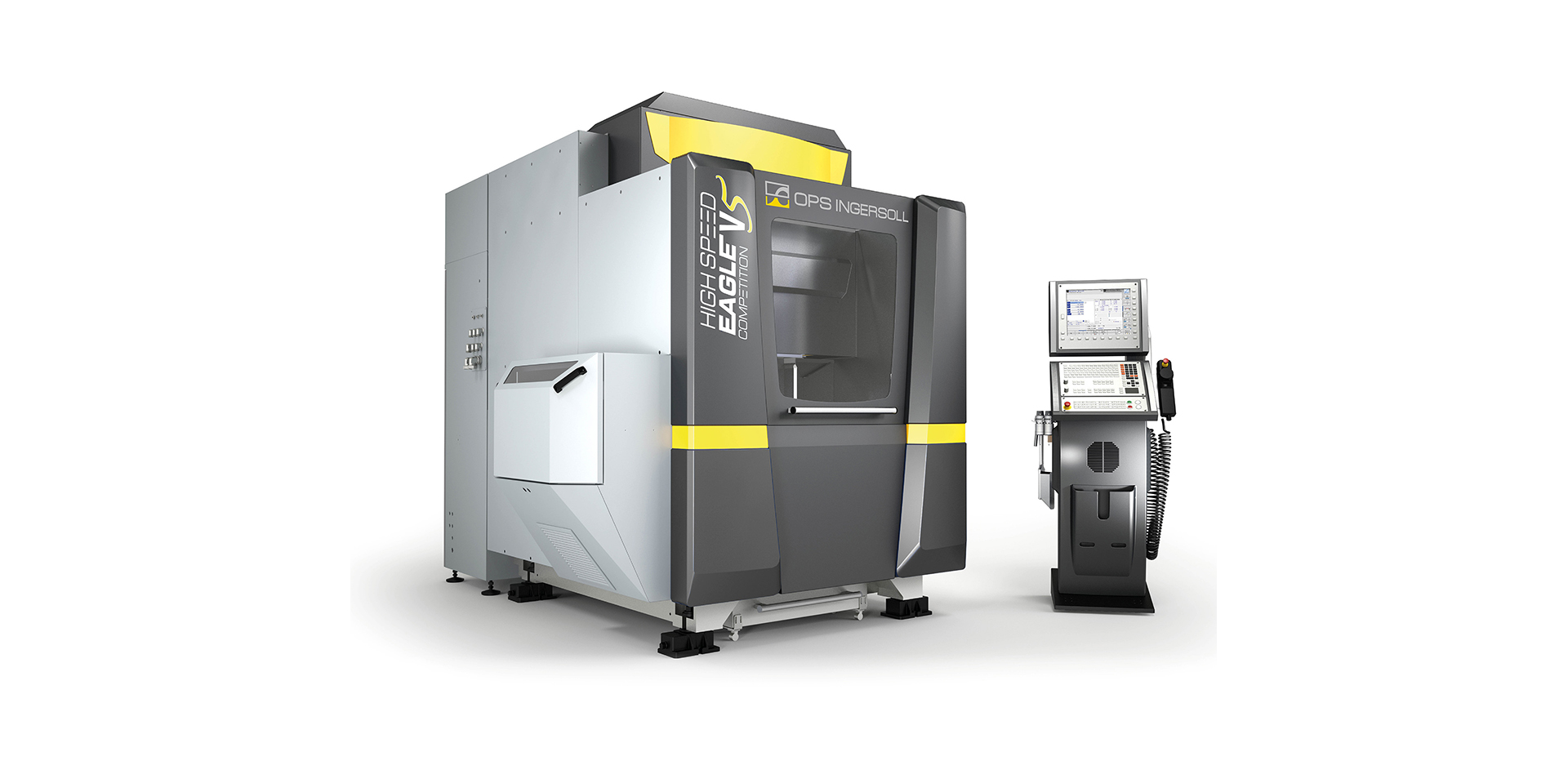
HIGH SPEED EAGLE V5
High dynamic precision milling machine
High dynamic precision milling machine
Compact precision
EAGLETec
inside
The HIGH SPEED EAGLE V5 can be used flexibly for small and medium-sized workpieces. Complex contours and geometries can be produced in a single setup. With the HIGH SPEED EAGLE V5, you can machine your graphite electrodes and other dusty materials with maximum precision and without reworking. It is also ideal for the precision machining of steel parts.
Setup HIGH SPEED EAGLE V5
Maximum cutting performance with 3-, 4- or 5-axis machining with the best surface quality: The HIGH SPEED EAGLE V5 sets standards in hard machining - including innovative temperature management and full encapsulation.
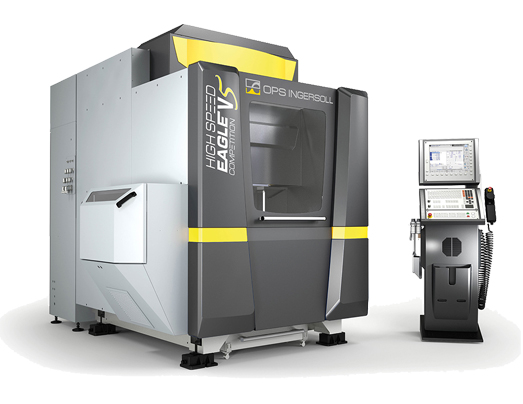
- Integrated tool changer 32 positions
- Flexible automation solutions possible, also as a retrofit
- HEIDENHAIN-Control TNC 640
max. 500 kg
max. 250 kg
Standard configuration
Technical data
min. 50 / max. 450 mm (with UPC-clamping system and pallet)
24/32 positions (HSK E50)
MultiTool 100/150 (optional)
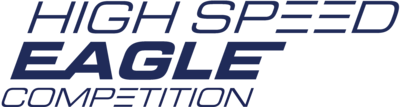
Equipment version
HIGH SPEED EAGLE Competition Line
High performer for flexible use
The Competition-Line already has active temperature control of the drive components and the HF spindle as standard. Increased precision and positioning accuracy is achieved through the use of calibrated measuring standards and laser interferometers. Integrated room temperature compensation ensures a reduction in thermal displacements.
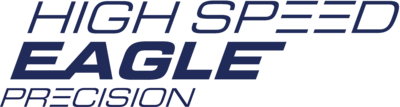
Equipment version
HIGH SPEED EAGLE Precision Line
Additional features for top precision
With our extensions to the Precision-Line, we also extract the last µm for precision machining: You can achieve an accuracy of less than 10 µm for 5-axis machining with active temperature control of all drive components. Maximum machining precision and repeatability thanks to geometric and thermal fine-tuning in the machine's working environment and volumetric measurement of the working area using LaserTracer. The dimensional accuracy between the milling machine and the customer's measuring machine is checked using a certified test standard.
Configuration
In addition to numerous integrated precision features, our HIGH SPEED V-Line machines can be perfectly equipped to your specific application with optional extensions.
Precision features







- PSC – Precision Spindle Compensation
- PGC – Position & Geometric Compensation
- IPR – Increase precision and repeatability (only available for Precision version)
- ACTC – Active Component Temperature Control, incl. HEIDENHAIN Option CTC (only available for Precision version)
- TCC – Tool Center Cycle (Cycle 320)
- AMC – Advanced Motion Control (Cycle 332)
- HPC – High Precision Cycle (Cycle 330)
HEIDENHAIN cycles




- 3D – TUNING CYCLE
- LAC – LOAD ADAPTIVE CONTROL
- DCM – DYNAMIC COLLISION CONTROL
- K-OPT – KINEMATICS-OPT
Further options
- Various control options from HEIDENHAIN
- Different HF spindles from Fischer and STEPTEC
- High precision CSC spindle with shaft cooling (only available for Precision version)
- MultiTool 100/150 Tool changer
- 4./5. axis with gear or torque drive
- Workpiece clamping systems from all well-known manufacturers
- Exhaust systems (graphite or oil mist)
- Aerosol dry lubrication
- Coolant management for wet machining
Coolant options
- Knoll Aerosol Master ATS4000
- MHT medium distributer
- Knoll coolantwater management
- Wet machining of graphite
Coolant options
- MultiChange easy
- MultiChange light/perfomance for the connection of up to 2 machines
- Preparation (interfaces) for third-party automation systems, e.g. EROWA, INDUNORM
- Jobmanagementsoftware, e.g. EVOMECS, CERTA, SOFLEX
'Dimensional' precision guarantee!
We use a machine bed made of polymer concrete for all our high speed milling machines. This mineral casting has outstanding physical properties for use in the static foundation in the high-precision range.
- Very insensitive to temperature fluctuations in the room environment. Even in non-air-conditioned factory halls, there are no restrictions on processing accuracy
- Vibration damping and dynamic rigidity ensure unshakeable geometric stability
- Absolutely resistant to water, frost, dirt and chemicals
With automation into the next generation of precision machining
Our future-oriented automation solutions of the MultiChange handling systems ensure even greater efficiency, thanks to fully automatic and extremely time-saving changing systems for electrodes and workpiece pallets. Another advantage: Our MultiChange systems are able to handle the technology combination of high speed milling and spark erosion, even with several machines.