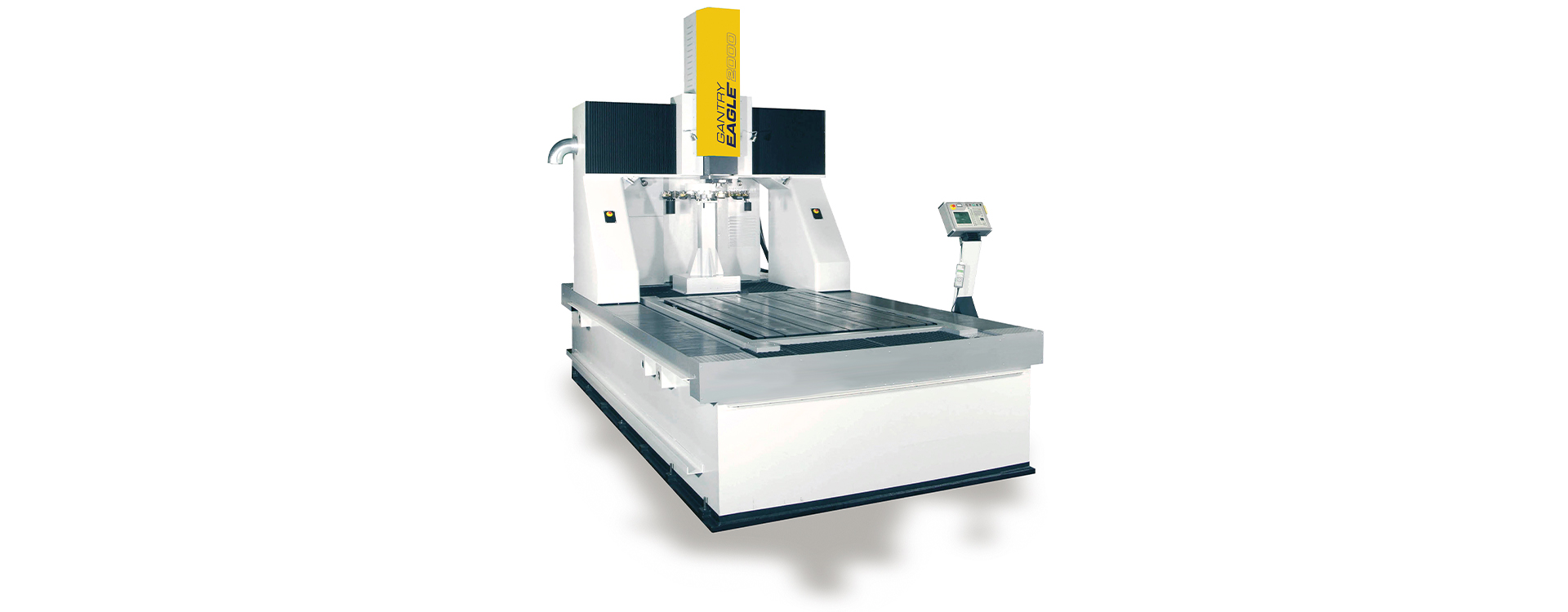
GANTRY EAGLE 2000
World's largest die-sinking EDM machine with lowerable work tank
World's largest die-sinking EDM machine with lowerable work tank
For largest applications – up to 30 t workpiece-weight
EAGLETec
inside
The GANTRY EAGLE 2000 meets all the requirements of large-scale mould making. The machine can be installed underground or on the floor and offers optimum accessibility for loading, set-up and inspection. It has large travel ranges with minimum space requirements. The big lifting container can be fully lowered into the base. Leakage protection is ensured by the positioning of the filter system and the dielectric supply in the machine base.
Setup GANTRY EAGLE 2000
In combination with the lowerable tank, the ergonomical working height, the integrated C-axis and the electrode changer, the GANTRY EAGLE 2000 offers you functional, excellent quality and a high level of operating comfort.
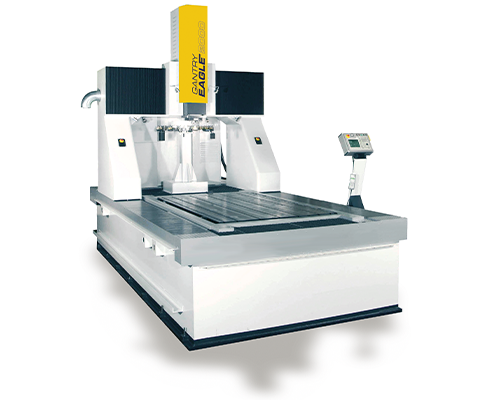
- High workpiece weights due to static storage on the table
- Program-controlled movement of filled lifting container
- Quick set-up and automatic level adjustment
C = 360°
max. 30.000 kg
Standard configuration
Technical data
programmable/automatic
Configuration
In addition to numerous precision features, our EAGLE G-Line machines can be perfectly equipped to your specific application with optional extensions.
Precision features




- ADC – Active Dielectric Cooling
- PGC – Position- & Geometric Compensation
- TC – Temperature Compensation
- IPR – Increase Precision & Repeatability
Included in the standard version
- EAGLE PowerTEC fine finish generator PT60
- EAGLE PowerJUMP with 18m/min intrval speed in the Z-axis
- Linear measuring system in all axes
- ECOTEC energy saving function
- C-axis
- Electrode changer 20 positions
- Pressure flushing programmable, suction connection manually
- Filter unit, 64m² paper filter
- CO2 fire-extinguishing system
Further options (selection)
- Generator 110 amps
- Technology package for fine finish and carbide machining
- Special software options for e.g. eroding without dielectric coverage (BA4)
- Electrode and workpiece clamping systems from all well-known manufacturers
- 30/48 position electrode changer
- RAM clamping system with optional 4/18 electrode changer
- Oil mist suction unit
Automation extensions
- MultiChange light/perfomance for the connection of up to 2 machines
- Preparation (interfaces) for third-party automation systems, e.g. EROWA, INDUNORM
- Jobmanagementsoftware, e.g. EVOMECS, CERTA, SOFLEX
With automation into the next generation of precision machining
Our future-oriented automation solutions of the MultiChange handling systems ensure even greater efficiency, thanks to fully automatic and extremely time-saving changing systems for electrodes and workpiece pallets. Another advantage: Our MultiChange systems are able to handle the technology combination of high speed milling and spark erosion, even with several machines.